Plastics can be found in all areas of life, such as packaging, automobiles, textiles, tools, toys, multimedia, etc.
The advantage of plastics is that their technical properties, such as elasticity, hardness, temperature and chemical resistance, can be modified in a variety of ways using different raw materials, manufacturing processes and additives.
The most commonly used polymers are polyethylene (PE), polypropylene (PP), polyvinyl chloride (PVC), polystyrene (PS), polyurethane (PUR) and polyethylene terephthalate (PET).
3D printing process for polymers
Injection molding, often also referred to as injection molding or injection molding process, which is based on primary molding. In this process, the injection molding machine liquefies the plastic, which is in the form of granules, and injects it under pressure into the corresponding mold. In this mold, the material cools down and returns to its solid state. The finished object can then be removed from the mold and, if necessary, reworked. The advantage of this process is that the original molds can be reused and very high volumes can be produced quickly and cost-effectively.
Increasingly, however, additive manufacturing is also being used to produce plastic parts. The advantage is that 3D printers are much smaller than injection molding machines, there is no need to make and replace master molds, and no special tools are required. Additive manufacturing is particularly useful when producing parts in small quantities or with more complex geometry. Accordingly, the printing processes are excellent for making prototypes and models or special tools.
In the meantime, 3D printers have reached production maturity and can also be used relatively inexpensively for private use. This means, therefore, that the additive manufacturing of plastic parts is used in very many areas, such as industry, research, construction, art, industry and also in the home.
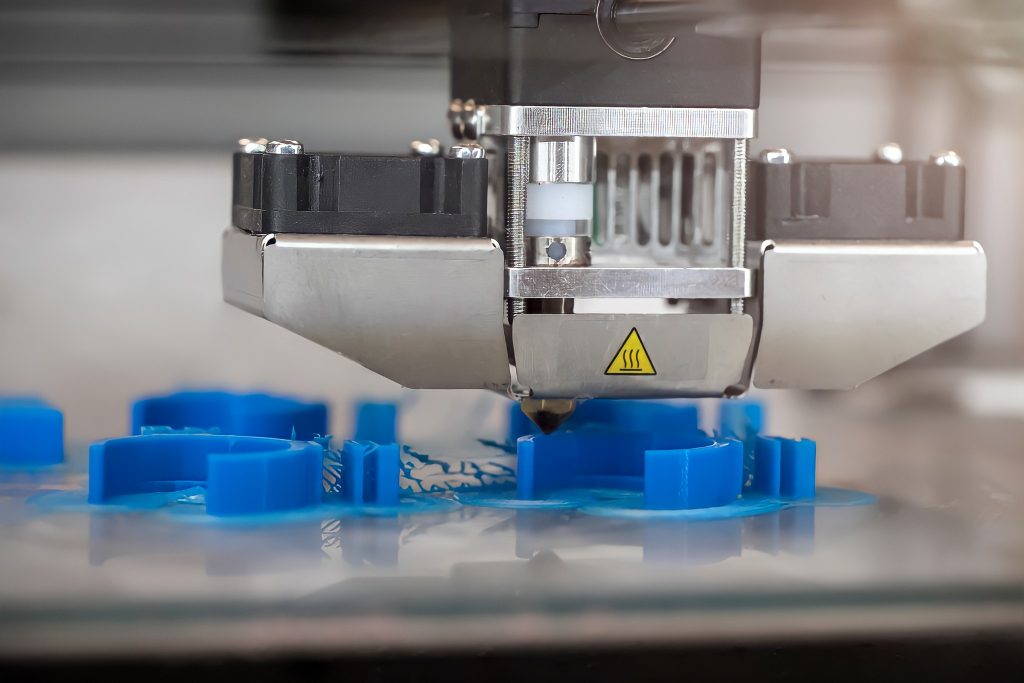
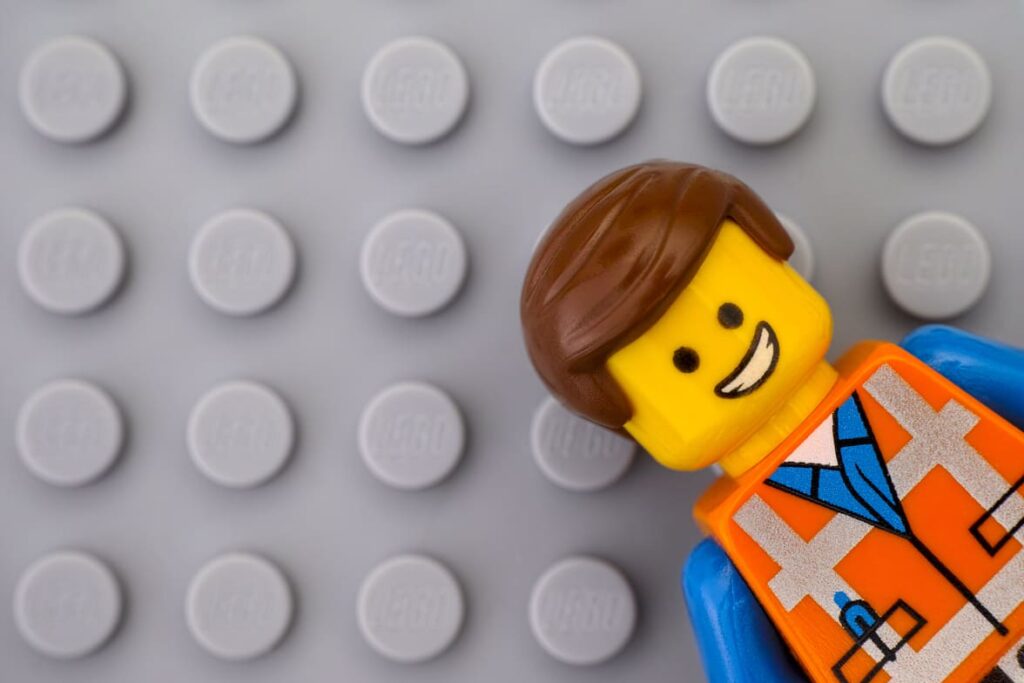
Fused Deposition Modeling (FDM)/ Fused Filament Fabrication (FFF)
Among the most commonly used polymer 3D printing processes is material extrusion, such as fused deposition modeling (FDM) or fused filament fabrication (FFF). In this process, a filament of a solid thermoplastic material is melted by forcing it through a heated extruder die. The material is then placed on the print bed in the path specified by the model, on which the filament then cools to form a layer. This process is repeated layer by layer until the component is completely manufactured. The thermoplastic filaments are usually made of PLA, ABS, PET or PETG.
Photopolymerisation
Another common process is bath-based photopolymerization (Vat photopolymerization), in which a light source selectively cures a photopolymer resin in a tank. This method includes stereolithography (SLA) and digital light processing (DLP). The main difference between the two is the light source, SLA uses laser dots and DLP uses a light projector.
There are other processes that can be considered for additive manufacturing of plastics, such as powder bed-based melting, which includes selective laser sintering (SLS).
In this process, a thermal energy source (laser) melts powder particles in the construction area and then a new layer of powder is applied and the process is repeated. One advantage of this is that the unused powder around the component supports the structure and can then be reused. Thermoplastic powder, such as nylon, is used here.
In free-jet material jetting, photopolymers or waxes are often used. The printer selectively deposits material droplets on the print bed or on the previous layer, which are then cured. In this process, different materials can also be used simultaneously for the same object. This is particularly advantageous for complex components that require a support structure.
Depending on the requirements of the components to be printed, various polymers can be considered, which differ in their optical, mechanical and thermal properties as well as the degree of difficulty of printing. The most commonly used materials for 3D printing are PLA (polylactic acid), a biodegradable plastic made from corn starch derivatives that is easy to print, and the petroleum-based ABS (acrylonitrile butadiene styrene). The latter is very robust and durable and is used, for example, for vehicle interiors or for toys.
Furthermore, PET, PETG (PET combined with glycol), nylon, polypropylene (PP), or even PMMA (also known as acrylic glass, Plexiglas) are also used. These materials can be modified in their appearance and properties with additives such as metals, ceramics, carbon, or wood, so that, for example, electrically conductive or magnetic filaments can be developed for 3D printing for special applications. Another group of polymers used are photopoylmers, or resins, which are cured layer by layer by UV light.
Printing problems include clogged extruder glands, cracks, warpage or deformation of the part, and adhesion problems between layers. To avoid these, it is important to know the properties of the material to be used. In particular, the glass transition temperature and the melting temperature are relevant. The temperature of the print bed should be below the glass transition temperature in order not to disturb the printing process. The extrusion temperature must be well above the melting point so that the polymer is liquid and proper printing can be ensured.
Studying thermal properties is an inevitable step in adjusting 3D printing settings to avoid errors and problems. For example, the glass point and the melting and crystallization point can be determined with the Differential Scanning Calorimeter (DSC). Analysis with a dilatometer (DIL) is also helpful here, as both the glass point and coefficient of thermal expansion (CTE) can be determined and deformation during heating and cooling can be studied. In addition, it is relevant to record the thermal and mechanical properties of the finished component, as these can differ significantly from raw material.
In particular, the thermal conductivity of a 3D printed body can differ significantly from a conventionally manufactured part due to the layered structure, which introduces additional thermal contact resistances, and the introduction of cavities. The Laser Flash Method (LFA), the Transient Hot Bridge (THB) and the Thermal Interface Materials (TIM) tester are suitable for this analysis.