Unleashing the potential of battery analytics – battery applications
Table of Contents
Maximising the efficiency and safety of batteries
In a world increasingly characterised by energy dependency, batteries play a crucial role in a sustainable future. Our precise analytical tools are designed to improve the efficiency and safety of batteries while extending their useful life.
The advanced technologies aim to push the boundaries of what is possible in battery analytics while contributing to a greener world. The aim is to explore how batteries can perform better, last longer and be safer.
Technological advances and advantages based on the development of car and mobile phone batteries
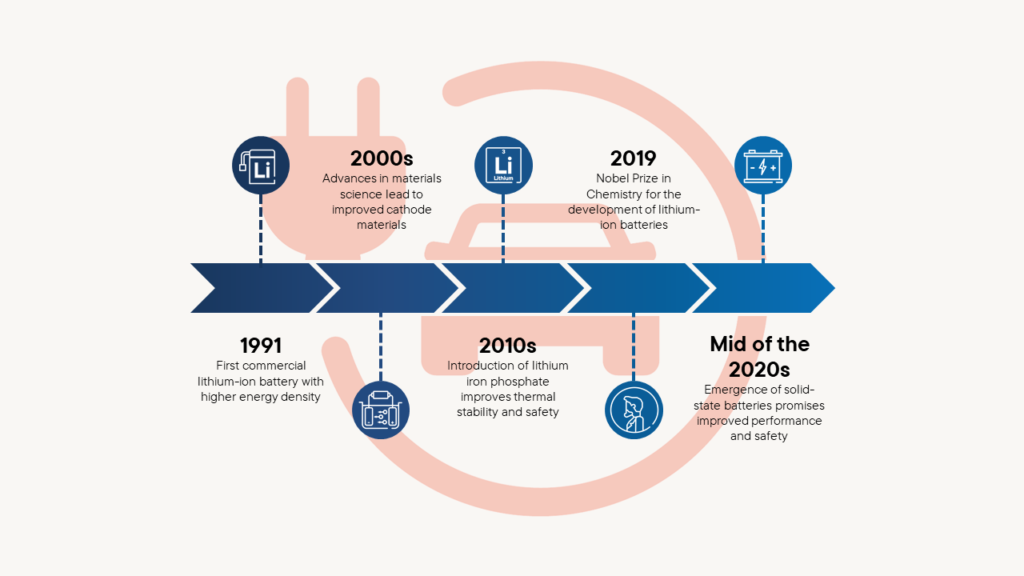
Introduction to the cell chemistry of batteries
Cell chemistry is the fundamental principle behind the functioning and performance characteristics of batteries. It comprises a complex interplay of electrochemical processes and material sciences that form the basis for energy storage and release.
In this interplay, the main components of a battery – cathode, anode, electrolyte and separator – act in a finely tuned manner to store and efficiently release electrical energy.
The cathode and anode, the electrochemical counterparts in a battery cell, determine key parameters such as cell voltage, energy capacity and cycle stability through their material-dependent redox properties.
Materials for the cathode, such as lithium cobalt oxides or lithium iron phosphate, and anode materials, including graphite and silicon-based composites, are the subject of intensive research in order to achieve optimum properties in terms of energy efficiency and density.
The electrolyte, an essential component for the transfer of ions between cathode and anode, significantly influences the ion dynamics and thus the overall performance of the battery.
The development of innovative electrolytes that ensure efficient ion transfer and at the same time increase the thermal and chemical stability of the battery is a central field of research.
This includes the investigation of both liquid and solid electrolyte formulations. The separator, a microporous layer that spatially separates the cathode and anode, is crucial for preventing internal short circuits.
Its permeability and mechanical integrity are crucial for the safety and longevity of the battery. An advanced separator design helps to improve ion diffusion and minimises the risk of thermal destabilisation.
The latest research approaches in battery technology, such as the development of solid-state electrolytes and lithium-sulphur batteries, aim to push the boundaries of conventional lithium-ion technologies.
Unlike conventional lithium-ion batteries, which use liquid electrolytes, solid-state electrolytes are made of a solid material that can still conduct ions.
These solid-state electrolytes eliminate many of the disadvantages of liquid electrolytes, such as the risk of leakage or flammability.
The advantages of solid-state electrolytes include:
1. increased energy density: the use of solid-state electrolytes allows the battery to store more energy in a smaller area, resulting in a higher energy density.
2. improved safety: solid-state electrolytes are typically non-flammable, reducing the risk of battery fires and thermal runaway.
3. longer life: Solid-state electrolytes are less prone to degradation over time, resulting in a longer battery life.
4. faster charging times: Some solid-state electrolytes allow for faster ion movement, which can lead to shorter battery charging times.
Analysing the cathode using differential scanning calorimetry
The performance and safety of lithium-ion batteries are largely dependent on the quality and properties of their material components.
Precise characterisation of these components is therefore crucial in order to make batteries more efficient, durable and safe.
Sophisticated measuring devices play a key role in this optimisation process.
The cathode, anode, separator and electrolyte can be analysed in detail using the broad LINSEIS product portfolio and devices such as the DSC, calorimeter or coupling with a mass spectrometer to obtain detailed information about the processes taking place during the charging and discharging of storage materials.
This detailed understanding enables targeted optimisation of these components, which can significantly increase the efficiency, service life and safety of batteries.
- Cathode: The cathode plays a central role in batteries, as it directly determines the energy capacity and therefore the performance of the battery. It is the positive pole of the battery and is the place where ions are absorbed during the discharge process, resulting in the release of energy.
- Material composition: Modern cathodes consist of various compounds such as lithium cobalt oxide (LiCoO2), lithium iron phosphate (LiFe-PO4), lithium nickel manganese cobalt oxide (NMC) and others.
- Crystal structure: The crystal structure of the cathode material plays a decisive role in the performance of the battery. It influences the mobility of the ions within the material and thus the speed of charging and discharging.
- Electrochemical stability: The electrochemical stability of the cathode is decisive for the service life of the battery. Materials with high electrochemical stability are less prone to capacity-reducing reactions during the charge/discharge cycle.
- Surface chemistry: The surface chemistry of the cathode material can influence the interaction with the electrolyte and thus affect the performance and stability of the battery. Optimising the surface chemistry can help to improve energy density and cycle stability.
- Thermal conductivity: The thermal conductivity of the cathode in batteries is crucial for thermal management to prevent overheating and potential safety risks. High thermal conductivity enables the efficient dissipation of heat generated during operation, keeping the temperature stable and preventing uncontrolled temperature rise, such as thermal runaway. Therefore, the selection of cathode materials and structures with good thermal conductivity is crucial for the performance and safety of battery systems.
TGA analysis of lithium iron phosphate (LiFePO4) to characterise the cathode
A striking example of the use of TGA is the analysis of lithium iron phosphate (LiFePO4), a widely used cathode material in lithium-ion batteries.
LiFePO4 is known for its high thermal stability and safety. In TGA analysis, a sample of LiFePO4 is heated in a controlled manner to assess its thermal stability and composition.
During the heating process, changes in the weight of the sample are precisely measured to obtain information about thermal decomposition processes. This data is crucial for understanding the thermal properties of the material, which is of great importance for applications in areas such as electromobility or stationary energy storage.
The TGA results provide important insights into the stability of the cathode material under operating conditions. For example, by analysing the decomposition temperatures of LiFePO4, conclusions can be drawn about the service life and safety of the battery under different operating conditions.
This enables targeted optimisation of the material composition and cell design in order to improve the overall performance and safety of the battery. The precise characterisation of cathode materials using thermogravimetric analysis is therefore an indispensable step towards increasing the performance and safety of lithium-ion batteries. Such analyses contribute significantly to the further development and optimisation of this key technology.
- Anode: In batteries, the anode acts as the negative pole and is largely responsible for the charging speed and capacity of the battery. During the charging process, ions from the cathode are stored in the anode, whereby the anode plays a key role in the storage and release of these ions.
- Material selection: Traditionally, graphite has been used as the anode material due to its ability to efficiently store ions. However, recent research is exploring alternative materials such as silicon, lithium titanate and various carbon nanomaterials that can provide higher capacity and faster charging speeds.
- Surface structure and porosity: The microstructure and porosity of anode materials are critical for ion storage. An optimised structure enables efficient ion mobility and contributes to a higher charging capacity.
- Electrochemical stability: The stability of the anode materials during the charge/discharge cycles is essential for the service life of the battery. Materials that are resistant to electrochemical degradation improve the cycling stability of the battery.
- Interaction with the electrolyte: The chemical interaction between the anode material and the electrolyte influences the performance of the battery. Optimised compatibility reduces undesirable side reactions that can lead to a reduction in capacity.
STA analysis of graphite anode materials
A concrete example of the application of STA is the analysis of graphite anode materials. Graphite is often used in lithium-ion batteries and is known for its ability to store lithium ions efficiently.
In STA, the graphite anode material is simultaneously subjected to differential thermal analysis (DTA) and thermogravimetry (TGA). This combined analysis provides valuable information about the thermal and mass-changing reactions of the material during heating.
The DTA component measures the heat flow to identify endothermic and exothermic events, while the TGA records the weight loss of the material, allowing conclusions to be drawn about decomposition temperatures and processes.
This comprehensive analysis can provide critical information about the stability of the anode material under different operating conditions. For example, identifying the temperature at which the graphite begins to oxidise enables the battery management system to be optimised in order to avoid overheating and increase the service life of the battery.
Furthermore, by analysing the thermal expansion and contraction of the graphite during lithium-ion intercalation, insights can be gained into the structural stability of the material and its influence on cycle stability.
The intercalation of lithium ions into the graphite anode material is a process in which lithium is deposited between the graphite layers, which leads to a change in volume. This volume change can be precisely determined using dilatometry, a method for measuring the change in length of materials as a function of temperature.
A dilatometer is the measuring device that records the thermal expansion and contraction of the graphite during lithium intercalation and thus provides insights into the structural stability of the anode material.
The use of Simultaneous Thermal Analysis to analyse the anode materials is also an essential step towards increasing the efficiency and lifetime of lithium-ion batteries.
These in-depth analyses are crucial in order to develop optimised materials for the requirements of modern battery technologies.
- Separator: In batteries, the separator fulfils a crucial safety function, particularly with regard to the risk of short circuits and thermal runaways. It is a microporous membrane that is placed between the cathode and anode to prevent direct contact and thus electrical short circuits between the electrodes. At the same time, it enables the flow of ions between the cathode and anode during the charging and discharging cycle.
- Ion permeability: The separator must have a high ion permeability to enable efficient ion transfer. This is crucial for the overall performance of the battery.
- Thermal and mechanical stability: The separator must be thermally and mechanically stable under the operating conditions of the battery. Insufficient thermal stability can lead to melting of the separator and thus to a short circuit, which represents a high safety risk.
- Ceramic coatings: Modern separators are often coated with ceramic particles to improve thermal stability. These coatings increase the melting integrity and mechanical robustness of the separator, especially at high temperatures, which significantly increases the safety of the battery. The melt integrity of a battery separator can be characterised using a thermomechanical analyser (TMA) to ensure that the separator does not mechanically fail or crack, which can lead to thermal runaway of the battery.
- Methods of analysis: An electromechanical measurement method is used to assess the properties of separators. These methods can provide information about the change in size of the separator under different operating conditions and the temperature at which the separator begins to fail.
- Role in preventing thermal runaway: An efficient and safe separator is critical to minimise the risk of thermal runaway. It must maintain a sufficient barrier effect even when the battery is exposed to extreme temperatures.
TMA measurement of coated separator membranes
A relevant example for the application of thermomechanical analysis (TMA) is the investigation of separator membranes coated with ceramic particles. This coating can significantly increase the safety of batteries by improving the melting integrity and mechanical robustness of the separator above its melting point.
The thermomechanical analysis (TMA) of battery separators primarily measures the physical reaction of the material to temperature-related changes. The key measured variables here are the expansion or contraction (elongation or shrinkage) of the separator material as a function of temperature.
The TMA measurement includes the following aspects:
- Measurement of the expansion coefficients: The TMA measures how the separator membrane physically changes under controlled temperature conditions. This includes the linear expansion or contraction of the material with temperature changes, which provides information about the thermal expansion coefficients.
- Mechanical integrity assessment: Measuring the expansion or contraction of the separator at different temperatures enables the assessment of its mechanical integrity. This is crucial to understand how the separator reacts under the thermal conditions of battery operation.
- Melting point determination: In addition to expansion, TMA can also be used to determine the melting point of the separator material. The melting point is a critical temperature at which the separator begins to lose its structural integrity, which can lead to safety risks.
- Electrolyte: In batteries, the electrolyte is a key element that is essential for the transport of ions between the cathode and anode. In most cases, it consists of a lithium salt solution in an organic solvent and enables the movement of lithium ions during the charging and discharging process of the battery.
- Ion conductivity: The conductivity of the electrolyte is crucial for the efficiency of ion transfer between the electrodes. High ionic conductivity allows the battery to charge and discharge quickly and improves overall performance
- Chemical composition: The chemical composition of the electrolyte, in particular the type of lithium salt and solvent, influences the electrochemical properties of the battery. The choice of components has a direct influence on factors such as the operating voltage, temperature stability and safety of the battery.
- Electrochemical stability: The electrolyte must be electrochemically stable in order to avoid decomposition at the battery’s operating voltages. An unstable electrolyte composition can lead to undesirable side reactions that impair the performance and service life of the battery.
- Interaction with electrode materials: The interaction of the electrolyte with the electrode materials is crucial for the long-term stability of the battery. Optimal interaction minimises the formation of damaging surface layers on the electrodes, known as “solid electrolyte interphase” (SEI).
- Thermal stability: The thermal stability of a battery electrolyte is a critical factor that significantly influences the operational safety and performance of batteries. A high thermal stability of the electrolyte ensures that the chemical integrity of the electrolyte and thus the ionic conductivity are maintained even with increasing operating temperatures or external thermal loads. The measurement of thermal stability, typically carried out using a dynamic differential scanning calorimeter (DSC) or thermogravimetric analysis (TGA), enables the identification of temperature limits within which the electrolyte is stable and does not release any dangerous decomposition products. This is essential to minimise safety risks such as thermal runaway and to ensure a safe operating environment for the battery.
TGA-MS measurement of electrolytes
A concrete example of the application of TGA is the investigation of the thermal stability and composition of electrolytes in lithium-ion batteries.
In this measurement, the electrolyte is exposed to a controlled temperature increase in order to analyse its thermal decomposition and the resulting weight loss.
This data is particularly useful for understanding the stability of the electrolyte under different operating conditions.
For example, the decomposition temperature of the electrolyte can provide information on the temperatures at which the battery can be safely operated without the risk of thermal degradation of the electrolyte. Thermal degradation of the electrolyte is a process in which the electrolyte decomposes under the influence of high temperatures.
This can be critical for several reasons:
1. decomposition temperature: Determining the decomposition temperature of the electrolyte provides information on the temperatures at which the battery can be operated safely. The decomposition temperature is the threshold at which the electrolyte begins to change chemically and degrade.
2. risk of thermal degradation: If the decomposition temperature is exceeded, the electrolyte can become unstable and undergo chemical reactions that impair the performance and safety of the battery. This can also lead to the formation of gases and a potential increase in pressure within the battery cell.
3. effects on battery performance: thermal degradation of the electrolyte can lead to a reduction in ionic conductivity and thus to reduced battery efficiency. In addition, the degradation of the electrolyte can lead to the formation of harmful products that affect the electrode surfaces.
4 Safety aspects: The thermal stability of the electrolyte is crucial for the overall safety of the battery. Thermal degradation can increase the risk of thermal runaway, especially if there is a reaction with other battery components.
Furthermore, TGA-MS can be used to determine the composition of the electrolyte, including the content of solvents and other additives.
This information is crucial for optimising the ion transport properties of the electrolyte, which in turn can positively influence the efficiency and service life of the battery.
The precise characterisation of the electrolyte using thermogravimetric analysis provides essential findings for the development of more efficient and safer batteries. The data obtained from these analyses enables targeted optimisation of the battery components, which leads to improved overall battery performance.
Each of these components contributes significantly to the overall performance and safety of a lithium-ion battery. The precise characterisation by Linseis’ measuring devices enables targeted optimisation of these components, which can significantly increase the efficiency, service life and safety of batteries.
Preventing thermal runaway – safety first
Thermal runaway, an uncontrolled rise in temperature in batteries, can lead to serious safety problems.
The analysers used to study the thermal and mechanical stability of battery materials are crucial to minimising the risks of such an event. They provide precise insights into the thermal stability of battery materials and help to identify potential sources of danger.
Thermal runaway occurs when the temperature within a battery cell reaches a point where the heat generated is greater than the heat released. This can lead to a chain reaction that destroys the battery or even causes fires. It is important to understand the causes of thermal runaway and take appropriate measures to minimise the risk.
- Early detection with DSC and TGA: Early detection of conditions that could lead to a thermal runaway is crucial. Instruments such as the Differential Scanning Calorimeter (DSC ) and Thermogravimetric Analysis (TGA) provide important data on the thermal behaviour of battery materials. They help to identify critical temperature ranges at which the materials become unstable.
- Analysing the causes: Analysing the causes of a thermal runaway involves investigating material compositions, electrolyte stability and internal cell reactions. These analyses provide valuable insights to identify potential risk factors and develop appropriate countermeasures.
- Safety assessment: By measuring heat generation and thermal management, the instruments can assess the safety standards of batteries. This is particularly important in the development of batteries for high-performance applications such as electric vehicles or energy storage systems.
- Material optimisation: The analysis results support the selection and development of materials that are less susceptible to thermal runaway. This contributes to improved overall safety, optimised heat dissipation from the battery cell and battery reliability.
- Optimisation of electrolytes: Optimisation of electrolyte composition is another important aspect that is supported by precise instruments. An improved electrolyte formulation based on analytical data can help to increase the thermal stability within the cell, which in turn increases the safety of the battery.
- Optimising the cell design: Optimising the cell design to prevent thermal runaway requires integrated thermal management based on a careful selection of materials that efficiently regulate heat dissipation and absorption. Scientifically selected anode and cathode materials with high thermal conductivities as well as thermally stable separators and electrolytes are crucial to avoid excessive heat generation. In addition, advanced cooling mechanisms and insulation materials contribute to heat distribution and insulation, preventing local overheating and homogenising the cell temperature. A well thought-out cell design that takes these components into account makes a significant contribution to increasing battery safety and minimising the risk of thermal runaway.
- Preventive measures through material characterisation: The implementation of preventive measures based on the analysis results is a decisive step towards minimising the risk of thermal runaway. This includes optimising the cell design, improving the battery management system and developing safety mechanisms.
Thermal management – risk minimisation and optimised thermal management for longer service life and efficiency
Efficient regulation of the operating temperature is a decisive factor for the performance and longevity of batteries. It helps to minimise the degradation of battery components and extend the overall service life.
Lithium-ion batteries have become the standard for portable electronics, electric vehicles and energy storage systems, mainly due to their high energy density and charge cycle stability.
The operating temperature is critical to the efficiency and longevity of these batteries, with the optimum temperature being between approximately 15°C and 35°C.
Temperatures above this range accelerate chemical degradation, increase the risk of thermal runaway and can lead to permanent loss of capacity.
Temperatures that are too low, on the other hand, impair ion diffusion and increase internal resistance, which reduces battery performance and increases the risk of lithium plating during charging.
Maintaining an appropriate operating temperature is therefore essential to ensure maximum performance, safety and battery life.
Various thermal management methods, such as active cooling or indirect liquid cooling, are crucial to keep the operating temperature in the optimal range to ensure the performance and safety of lithium-ion batteries.
Complexity of thermal management in battery technologies
- Thermal management in modern battery systems plays a decisive role in performance, safety and service life. It involves the precise regulation of internal temperature conditions to ensure optimum functionality.
- An uncontrolled increase in temperature can lead to irreversible damage through chemical degradation, while temperatures that are too low can impair the ionic conductivity and therefore the performance of the battery.
- Balanced thermal management ensures not only the efficiency but also the longevity and safety of batteries, especially in high-performance applications such as electric vehicles and energy storage systems.
Analytical instruments for thermal transport properties
- Advanced analytical instruments are used to analyse the thermal properties of battery materials. The Laser Flash Analyser (LFA), the Transient Hot Bridge (THB) and the Periodic Laser Heating (PLH).
- The LFA enables the measurement of thermal conductivity and diffusivity, which are crucial for heat transfer within the battery components.
- The Transient Hot Bridge (THB) extends the spectrum of thermal analysis by measuring the thermal conductivity and thermal resistance of battery materials under real operating conditions.
- Periodic Laser Heating (PLH) is an innovative method for fast and precise characterisation of thermal conductivity and specific heat capacity. It is essential for accurate thermal analysis and for the development of battery materials with superior thermal properties.
Importance of the TIM tester for efficient heat transfer
- The Thermal Interface Material (TIM) tester specialises in the evaluation of materials used at the interfaces between the battery cells and cooling components. It can also measure the thermal impedance, which enables the optimisation of the thermal management of cell arrays.
- He precisely measures the thermal conductivity and thermal resistance of these materials to ensure optimal heat transfer from the batteries to the housing or heat sink.
- Efficient interface materials, identified and optimised by the TIM tester, are essential to avoid overheating of the cells and contribute significantly to improving the overall performance of the battery.
Visualisation and interpretation of thermal data
- The visualisation of the data obtained through these analyses enables an in-depth interpretation of the thermal properties of the battery materials.
- Diagrams showing the thermal conductivity or specific heat capacity over different temperature ranges provide comprehensive insights into the thermal management of the batteries.
Effective thermal management, supported by precise measurements and analysis from Linseis’ instruments, is essential to maximise the performance, safety and lifetime of modern batteries.
Through continuous innovation in this area, we are helping to further improve the reliability and efficiency of battery technology.
The figure shows a measurement in which the LFA battery tests were carried out on a Na-ion cathode material. The thermal diffusivity and thermal conductivity reach a maximum at approx. 90 °C and then decrease relatively sharply.
Thermal stability – a key factor for reliable batteries
The thermal stability of battery materials is a key factor in the safety and reliability of lithium-ion batteries. Linseis’ state-of-the-art measurement equipment plays a central role in assessing and improving this important property.
The ability to accurately assess the thermal stability of battery materials is critical to ensure that modern batteries meet high safety and performance requirements. Linseis’ measurement devices provide the necessary precision and reliability to fully assess this important property.
The figure below shows a DSC measurement curve of a ceramic solid electrolyte used in solid-state batteries, enabling safer high-energy batteries. High temperature heat treatment is required to bond the electrolyte, electrodes and other components such as current collectors.
Device Characterisation – Precision in battery research with the battery calorimeter
A battery calorimeter is a device for measuring the heat generated by a battery during charging and discharging. This measurement is known as “heat of reaction” and is an important indicator of a battery’s performance. The heat of reaction is the difference between the enthalpy (heat content) of the reactants and the products of a chemical reaction.
Battery calorimeters are used in research and development to evaluate new battery chemistries and to optimise the design of existing batteries. They are also used in the manufacturing process to ensure that batteries meet performance and safety standards.
Linseis offers a modular calorimeter (IBC) for the thermal monitoring of batteries. It consists of a variable number of almost identical components and enables a wide range of battery cell sizes to be analysed. The geometry of the modules is also easily scalable.
Importance of the battery calorimeter: The battery calorimeter measures the amount of heat generated during electrochemical reactions within the battery. These measurements are crucial for understanding and improving the thermal behaviour and efficiency of batteries.
Areas of application: These devices are particularly important for the development of new battery types, such as lithium-ion batteries, where thermal stability and safety are of paramount importance. They are also used in quality control and performance testing of batteries.
Thermal analysis and safety: By analysing heat development under different operating conditions, battery calorimeters help to identify and prevent potential safety risks such as thermal runaway. This is crucial for the safety of end-user products.
Optimising battery performance: Accurate measurement of heat generation allows the internal chemistry and design of the battery to be optimised, resulting in increased energy density, improved charge capacity and longer life.
Research and development: Battery calorimeters are used in research and development laboratories to test and evaluate new materials and technologies. The resulting findings are essential for progress in battery technology.
Developed jointly with the Physikalisch-Technische Bundesanstalt: