Measurement in high purity atmospheres and high vacuum
Together with Fraunhofer IKTS, we have developed an optical dilatometer as part of a funded AiF-ZIM project, supported by the German Federal Ministry for Economic Affairs and Energy (BMWi). The dilatometer was designed to measure in temperatures up to 1600 °C and high vacuum (approx. 5 E-5 mbar). In addition, it achieves an oxygen content in dynamic atmospheres of approx. 0.5 ppm.
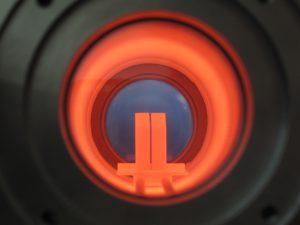
Optical dilatometers measure the dimensional changes of samples as a function of time and temperature. Together with hot-phase microscopes, they have a wide range of applications, fundamentally in materials and process development. For example, they are used to determine sintering processes and the behavior of thermal expansion, especially for anisotropic or brittle materials and samples with complex geometries. Optically, the wetting and spreading behavior on different substrates, are represented by the contact angle, allowing the determination of surface tension up to high temperatures. Furthermore, the investigation of contact corrosion between molten metal and glass, molten slag and ash in contact with ceramic and metallic materials is possible. Another important possibility is the characterization of infiltration, e.g. of molten metal into ceramic materials. The standardized optical dilatometers and heating microscopes are designed for measurements in air or atmospheres that have a high oxygen concentration.
The dilatometer was specially designed for the characterization of joining processes of ceramic-ceramic and ceramic-metal joints by active soldering. The new optical dilatometer enables the investigation of melting and wetting behavior on ceramic substrates of solder materials with oxygen affinity solder components such as titanium. With conventional hot-phase microscopes, surface oxidation occurs due to the presence of residual oxygen, which impedes wetting of the substrate by the solder or leads to falsified experimental results. The new experimental possibilities thus gained are an essential contribution to the fundamental understanding and further development and optimization of joining processes.
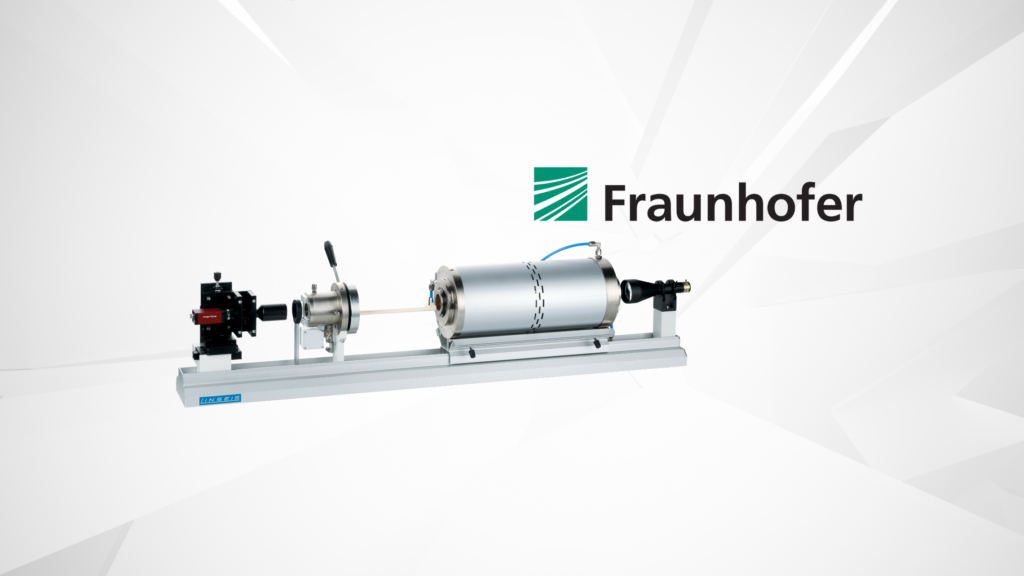