目次
金属はさまざまな産業分野で、ほとんどあらゆる用途に使用されている。
建築や自動車製造のほかにも、金属は次のような用途にも使われている。 導体や半導体コーティング、電子部品、あるいは電気工学におけるハウジング部品としても使用されている。
特にここでは、自動車産業において、 医療および 航空宇宙分野特に自動車、医療、航空宇宙分野では、用途が非常に特殊で、小型で精密にフィットする構造が要求されることが多い。
これらを実現するために、これまでますます近代的な製造方法が開発され、それぞれがより高い精度を低コストで実現し、材料消費量も少なくなっている。
特に、いわゆる3Dプリンティング工程は、この点で大きな進歩を遂げている。
金属による3Dプリントプロセス
直接レーザー金属焼結
金属を使った3Dプリンティング法の中でも、粉末床融合技術に基づくダイレクトレーザーメタル焼結(DMLS)は、レーザーパワーベッド融合(LPBF)としても知られ、特に著名である。 このプロセスでは、金属粉が供給され、通常はレーザーであるエネルギー源によって選択的に溶かされ、3D構造体が作られる。
同様の方法であるCLAD(レーザークラッディングまたはクラッディング、DED – direct energy deposition – プロセスとも)では、通常のプリンターのインクと同様に、ノズルから金属粉を堆積させる。 しかし、ノズルの出口では、粉末がレーザーによって直接溶かされるため、液体金属を直接印刷することができる。
アディティブ・マニュファクチャリングとアディティブ・マシニングを組み合わせたものに、いわゆる コールド・カッティング法またはコールド・ガス・スプレー法がある。 この方法では、微細な金属粒子を高圧のキャリアガス(通常はヘリウム)とともに微細なノズルから押し出し、基材に衝突させて塑性変形させ、実際に溶融させることなく直接加工できる層を形成する。 しかし、この方法はコストが高いため、ほとんど使われていない。
メタル・バインダー・ジェット
また メタルバインダージェッティング.プラスチックパウダーベッドプロセスと同様に、金属はバインダーと混合され、均質な塊を形成するために結合される。出来上がったグリーンパーツは、燃焼やレーザー加熱などの熱処理によってバインダーから解放され、最終的な形状になります。
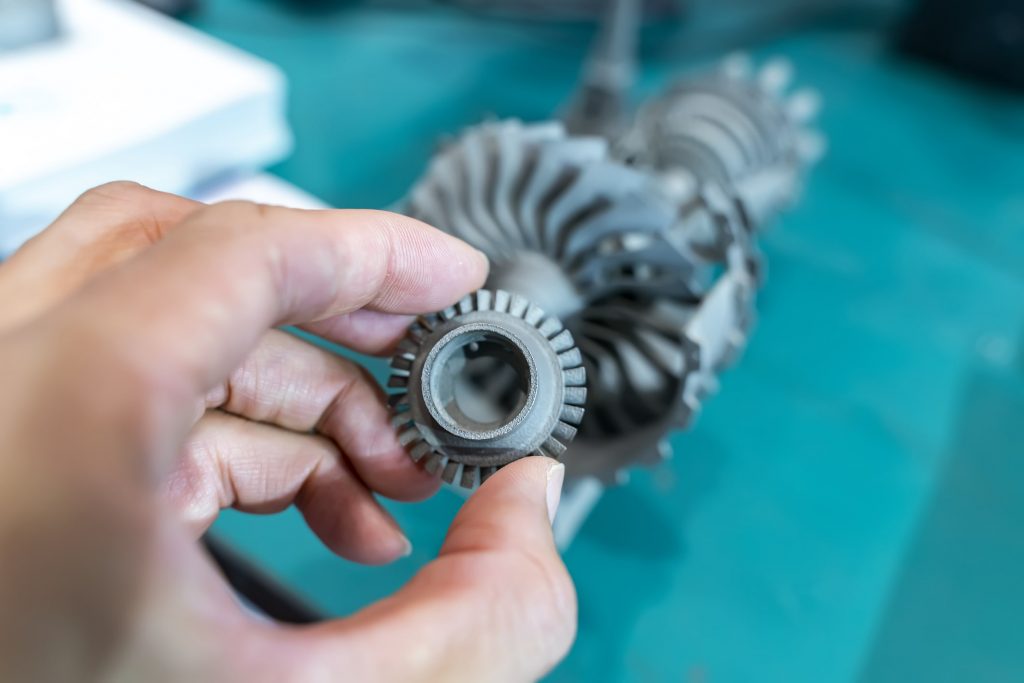
溶融堆積モデリング
プラスチック・プロセスと同様に、金属フィラメント(通常は低融点金属または合金製)を柔らかくなるまで加熱し、ノズルから層状に塗布する溶融積層造形(FDM)もある。
前述の方法はすべて、すべての金属で機能するわけではないという点で共通している。 メタリック3Dプリンティングの一般的な金属は、アルミニウムとその合金、鋼鉄、鉄合金、そしてガリウム、インジウム、チタン、コバルト、クロムなどの材料である。比較的高価ではあるが、現在では金や銀のような貴金属も使用されている。 しかし、これらの金属を成形するのはやや難しい。 重金属や非常に硬い金属、高融点金属は、ほとんど使われないか、まったく使われない。
金属3Dプリンティングの応用
メタリック3Dプリンティングの最も一般的な用途は、主にプロトタイピングと研究開発であり、特にシリーズではなく個々の部品のみを製造する場合である。 この場合、鋳造ワークピース用の金型は非常に高価であることが多く、3Dプリントによって巧みに回避することができる。
鋳造ワークピースと比べて節約できるエネルギーコストも大きい。 同様に、高価になりがちな金属原料の材料費も節約できます。 さらに、特に医療技術で個別に製造されたインプラントや、特別に適合された機械のスペアパーツでは、金属を使用した3Dプリントの利点は否定できません。
セラミックやポリマーの3Dプリンティングとは対照的に、金属焼結やコールド・ガス・プリンティングでは、金属によって融点が大きく異なるため、すべての形状や構造が容易に実現できるわけではなく、混合物や特定の層を適用することが常に可能とは限りません。 とはいえ、将来的にはさらに柔軟で多様なアプリケーションを実現するために、これらの方法に関する研究は現在進行中である。
金属を使った3Dプリントの利点:
- 工具不要
- エネルギーコストの節約
- 金属原料の節約
- 部品の個別製造が可能
3Dプリント金属の熱分析
熱分析は、生成された金属の特性に関する特徴を明らかにし、従来の製造方法と3Dプリントされたコンポーネントの違いや偏差を特定するのに役立ちます。