目次
3Dプリンティング・セラミックスの熱解析
セラミックスは、産業の多くの分野で使用されている。原則として、セラミックスはまず原料の塊からグリーン体として形成され、その後、この「グリーン体」を特殊な方法で処理・焼成(いわゆる焼結)して硬化させ、最終的な形状にします。
業種によっては、食器、装飾品、衛生陶器などのシンプルなものから、人工関節などのテクニカル・セラミック、あるいは様々な技術部品に至るまで様々です。
セラミック製品は通常、最初の機械的加工の後、窯で焼成されます。
900℃から1400℃の温度にさらされます。
これは、セラミックの焼成中の化学反応を制御し、水蒸気、二酸化炭素、その他の混和物の脱ガスを制御するために、一定の温度で一定の時間間隔で加熱するだけでなく、正確に定義された等温間隔で加熱することによって行われます。
最初の焼成の後、多くの場合、釉薬が陶磁器に加えられ、その後、作品を完全に硬化させるために再び焼成される。
全工程に数時間かかるため、少なからず時間がかかる。
さらに、焼成後に作品が破損せずに窯から出てくるという保証はありません。さまざまなエラー(材料の不足、焼成工程の誤りなど)が起こり、セラミックの破損やひび割れにつながる可能性があります。
多種多様なセラミック部品を焼成するための、より現代的でシンプルなソリューションが積層造形です。
セラミックの場合、これはしばしば3Dプリンティングと呼ばれます。
これは、材料を層ごとに塗布して三次元物体を作成する製造プロセスです。
造形は通常コンピュータ支援設計(CAD)で行われ、指定された寸法や形状に合わせて、1種類以上の液体または固体の材料が出発材料として使用される。
印刷プロセス、化学的な 硬化または溶融プロセス多くの場合、温度やレーザーによって制御されます。
モデルに3Dスキャナーを使用することも可能です。
従来の焼成プロセスに対するこの方法の利点は明らかである。セラミックを層状に塗布することで、焼成プロセス中に破損する危険性が特に高いフィリグリー構造や複雑な構造を製造することができる。
加えて、炉での焼成工程が不要なため、付加焼結や3Dプリンティングされたワークピースをより迅速に製造できるため、大幅な時間短縮が達成される。
切削加工、旋盤加工、穴あけ加工など、材料を除去するすべての工程と比較して、3Dプリンティングは、元の金型の後に追加の機械加工工程を省くことができるという利点がある。
ほとんどの場合、このプロセスはエネルギー効率も高く、特に材料が必要なサイズと質量で一度だけ造形する必要がある場合はなおさらである。
また、異なる材料を1台の機械で加工できるのも利点だ。
もともと、3Dプリンティングのプロセスは、ポリマー産業で最初に応用され、開発された。 ポリマー産業プラスチックは溶けて扱いやすく、焼結や硬化を必要としないからだ。軟化点ギリギリまで加熱し、プリントしたフィラメントを急速に冷却することで、リアルタイムで構造体を作ることができた。しかし、このプロセスは急速に進化し、さまざまなポリマーだけでなく、今では金属やセラミックもプリントできるようになり、3Dプリンティングは製造業の多用途な選択肢となっている。
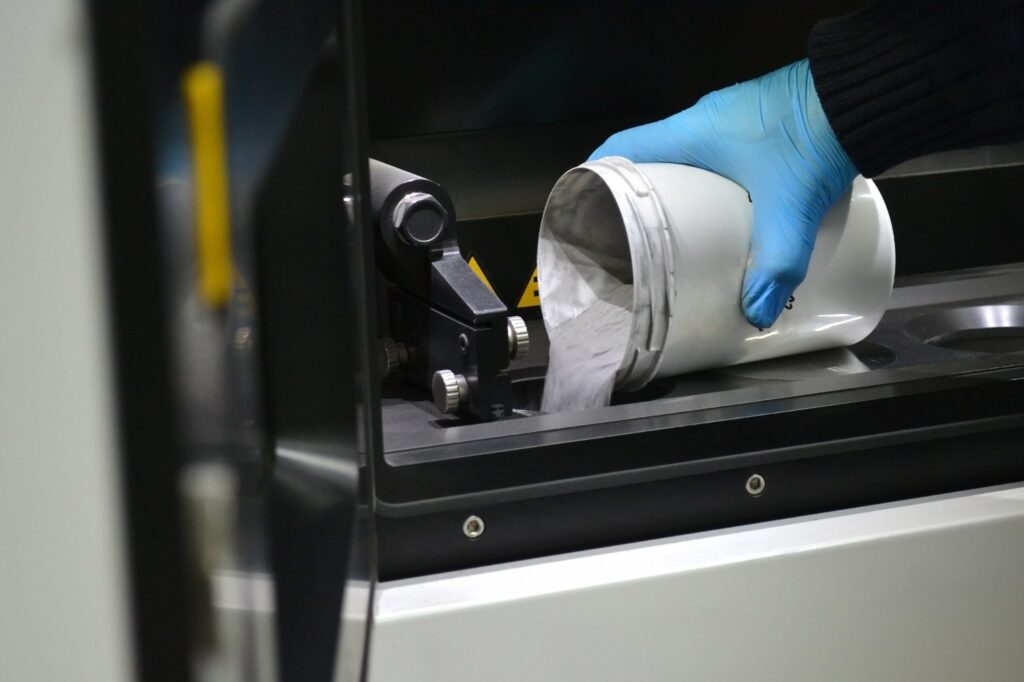
現在3Dプリンティングに使用されている代表的な材料には、プラスチック、セラミックス、金属、あるいはグラファイトなどの炭素化合物がある。 ここで最も重要な技術は、金属用のレーザービーム溶解と電子ビーム溶解、ポリマー、セラミックス、金属用のレーザー焼結、液体樹脂用のステレオリソグラフィーとデジタル光処理、プラスチックと樹脂用のポリジェットモデリングと溶融層モデリングである。
積層造形の製造工程は主に7つのカテゴリーに分けられ、現在ではいくつかの規格(DIN EN ISO/ASTM 52900、旧ASTM F2792)にも詳細に記載されている:
- バインダー出力
- 材料生産量
- パウダーベッド融合
- 材料押出
- 光重合
- ターゲット・エネルギー蒸着
- シートラミネート
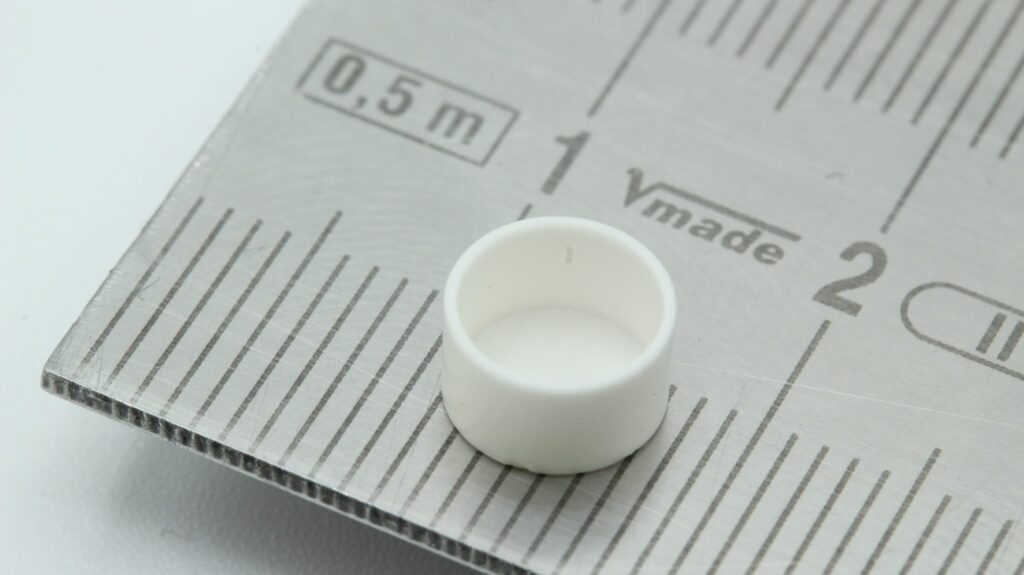
両者の主な違いは、パーツを作成するためにどのようにレイヤーを適用するか、そしてどのような材料を使用するかである。
マシンと3Dプリントプロセスを選択する上で最も重要な要素は、スピード(対象物のサイズによる)とコスト(材料とマシン)です。
一般的な材料:金属、セラミック、プラスチック。
アディティブ・マニュファクチャリング技術の主な応用分野は、やはり研究であり、とりわけ産業界における製品開発やプロトタイプの製作である。
特別な工具を必要とせず、図面からモデルへの変換が非常に短時間で実現できるため、モデル、プロトタイプ、ツール、または特定の製品の製造に理想的です。
その他の応用分野 医療技術特別に適合させた補綴物やインプラント(特に歯科)を製作する必要があり、多くの場合、個別にカスタマイズされる。しかし、彫刻や美術など、より珍しい分野では、積層造形で彫刻を製作することもある。一方、3Dプリンターは個人利用も可能である。プロセスとプリンターは現在、生産が成熟し、比較的低コストで一般に入手できるようになったからだ。特に家庭用では、玩具、スペアパーツ、小型ホルダーなどのプラスチック製品を、予備知識がなくても簡単に製造できる。
セラミックスの場合、3Dプリントには以下の方法が用いられる:
- 選択的レーザー焼結(SLS)などの粉末床溶融プロセス。 このプロセスは一般に、ポリマー、セラミック粉末、金属の印刷に使用できる。 このプロセスでは、材料の粉末を高エネルギーのレーザーで溶かし、完全に高密度な材料を層ごとに作ります。 粉末の薄い層は、ノズルを使ってトレイに置かれる。 その後、レーザーが粉末を局所的に焼結させ、最初の層を形成する。 このバリエーションとして、3Dインクジェット・プリンティングがある。 ここでは、インクジェットのようなプロセスで、パーツの断面にある粉末(石膏や樹脂)の層にバインダーを印刷する。 パウダーベッド融合技術の利点は、余分なパウダーがプリントされた物体の支持体として機能することである。
- FDM (Fused Deposition Modeling)またはFFF (Fused Filament Fabrication)は、所望のセラミックの小さなパトリックスを加工します。
- これを実現するために、フィラメントには特定のバインダーが使用され、通常はセラミック粉末をつなぎ合わせる特殊なプラスチックが使われる。その後、フィラメントを液化する程度に加熱し、従来のプラスチック・フィラメントと同じように印刷することができる。ここでのセラミック粒子の直径は約1~2μmである。
- そのため、プラスチックで印刷する際にノズルから直接出てくるので、目的のレイヤーを直接印刷することができる。
- この工程で溶けるのは、粉末をつなぎ合わせて運搬するプラスチックだけであり、バインダーの役割を果たす。 最終的な結果は印刷された型だが、それは固体のセラミック本体ではなく、本質的にはセラミック粉末であることに変わりはない。
- これはまだ最終製品ではなく、まず手直しが必要なグリーンコンパクトである。
- 最後に、特殊な工程でプラスチックの一部を除去する。 その後、特殊な炉の中で高温と化学物質にさらされる焼結工程が行われる。
- この工程で、セラミック部品は結合し、プラスチックは完全に除去されます。 このように、FDMは結局のところ、本来のセラミック焼成工程と非常によく似ています。
- これを実現するために、フィラメントには特定のバインダーが使用され、通常はセラミック粉末をつなぎ合わせる特殊なプラスチックが使われる。その後、フィラメントを液化する程度に加熱し、従来のプラスチック・フィラメントと同じように印刷することができる。ここでのセラミック粒子の直径は約1~2μmである。
3Dプリンターで使用する材料にとって適切な条件は、融解温度や温度下で材料がどのように膨張するか、あるいはどのような熱伝導性があるかといった温度挙動に左右される。
したがって、3Dプリンティングに使用する材料の熱特性を幅広く試験することは理にかなっています。
これらの調査には、以下の装置が関連します:
- クラシック ディラトメトリー (DIL)は、固体や粉末の熱線膨張や焼結挙動を広範囲に調査するために使用できます。このため、ダイラトメトリーは現在、セラミック製造における標準的な手順となっています。
- さらに、ワークピース内の温度分布と伝導をシミュレートし、制御するためには、熱伝導率を調査するためのさまざまな方法が有用である。
ここで最も一般的な方法は、以下のようなフラッシュ法です。 レーザーフラッシュ法(LFA)通常、固体や粉体の温度と熱伝導率は、高エネルギーの閃光を使用して測定することができます。
のような熱線法もあります。 トランジェント・ホット・ブリッジ (THB)などの熱線法もあり、室温で比較的迅速に信頼性の高い熱伝導値を得ることができます。
熱電対 トランスインターフェース材料テスター(TIM)のバリエーションである ガード付きホットプレートは、ペーストや粉体にも適しており、主に異なるバルク密度とその結果生じる熱輸送特性の変化を測定することができます。
.
コンポーネントが製造されると、そのコンポーネントの熱的・機械的特性要件を決定し、そのプロセスに特化した設計で開発することが重要になります。
これは通常、部品の製造工程に関係なく言えることです。
しかし、付加的に製造された部品の場合、機械的特性を確認することが特に必要である。
特にセラミックスの場合、焼結後または積層造形後にワークピースが大きく収縮し、材料不良につながるさまざまな欠陥の原因が考えられます。
ここでも通常、ダイラトメーターが使用され、状況によっては 熱機械分析(TMA)これは、曲げ試験、引張試験、圧縮試験によって機械的材料特性を正確に記録することができます。